Knuth Servomill 700 Servo Conventional Multipurpose Milling Machine ( Part No. 301250) The bestseller in the servo conventional class for workshop applications and single parts production
Knuth Servomill 700 Servo Conventional Multipurpose Milling Machine
( Part No. 301250)
The bestseller in the servo conventional class for workshop applications and single parts production
Availability. Currently 4 weeks from receipt of order. Subject to no prior sales.
Highlights
Knuth Servomill 700 Servo Conventional Multipurpose Milling Machine
The multi-purpose Servomill 700 milling machine offers a large working area with infinitely variable servo motor feed. With electronic handwheels and additional milling functions, the Servomill offers the advantages of modern CNC technology in conventional machining. Ideal for manufacturing or repair and training departments. The swiveling vertical milling head has a wide speed range for processing steel and non-ferrous metals. The extensive equipment also includes a pneumatic tool clamp.
- Swivel milling head with quill feed
- pneumatic tool tightening device
- infinitely variable spindle speed
- servo-conventional feed technology
- Ball screws in all axes
- Electronic handwheels
Details
Conventional milling easier, more precise and more efficient thanks to integrated electronics
- The Servomill machines represent a new generation of conventionally operated milling machines
- It is characterized by ease of use, significantly increased precision and increased processing performance
- The high reliability of all components used and their longevity significantly reduce the maintenance effort and thus ensure increased availability
- Solid machine frame in proven design, excellent stability and very careful processing
- Variable due to swiveling and movable upper beam
- Perfectly adjustable dovetail guide in the X-axis and wide square guides in the Y and Z directions
- Long-lasting precision thanks to ball screws in all axes
- All guides are hardened and ground and are supplied with slideway oil via a central lubrication system
- Swiveling milling head with pneumatic tool clamping and powerful 3.7 kW motor
- Infinitely variable spindle speed with reduction gear and LED speed display
- Manual quill feed with micrometer depth stop enables precise drilling, even at an angle
- Large, swiveling control panel with integrated position display
Servomill 700 highlights
- Control developed and manufactured in Germany
- Positioning control for traversing preselected distances in all axes
- Constant cutting speed, feed rate is based on the spindle speed
- Preloaded ball screws without backlash
- Servo motors in all axes, infinitely variable feed, rapid traverse and speed control
- Electronic spindle load indicator
- Electronic handwheels on all axes
- X, Y and Z axes can be moved using joystick technology
- Integrated position indicator with glass scales
Your advantages
- Simple: intuitive operation - clear arrangement of the operating elements and clear function
- Automatic feed infinitely adjustable in all axes
- Rapid traverse with up to 5000 mm/min
- End stops can be set electronically in each axis at the push of a button - 3 stop positions +/- per axis can be saved
- More precise: Operation via electronic handwheels - the axes are moved by high-quality servo drives, which implement your handwheel movements with the precision and dynamics of modern CNC machines
- More reliable: Drives, spindles and measuring systems are encapsulated or mounted in a protected manner and are almost maintenance-free
- Electronics - Made in Germany
- More resilient: only high-quality drive components are used that are designed for continuous operation
- Maintenance-free: no regular maintenance is required for the entire feed drive
- State-of-the-art feed technology:
- The axes are moved by high-quality servo drives that convert your hand wheel movements with the precision and dynamics of modern CNC machines
- Reliable, maintenance-free mass production technology
- High rapid traverse speed reduces idle times
- Ball screw drive in all axes:
- Decisively smaller loose error (backlash), which is reflected in significantly increased precision
- Significantly reduced friction, no stick-slip effect, reduced heat generation - less wear
- Electronic handwheels:
- Operation via electronic handwheels in the µ range - in terms of feel and position as with a conventional machine, but smoother and more precise
- Joystick operation:
- Ease of use when moving the axes
- Easy handling when editing work sequences
- Electronic fixed stops:
- In each axis, 3 x 2 end stops can be set electronically at the push of a button - these switches are grouped directly around the feed switch and can be operated intuitively
- When drilling coordinates or chamfering pockets, this ensures a high level of repeat accuracy and significantly more positions can be set up than with conventional machines
- Constant cutting speed:
- In addition to infinitely variable control of the feed rate, this can also be linked to the spindle speed, in a freely selectable ratio of feed per spindle revolution in the range from 0.01 to 1 mm/rev
- The technology value fz (feed/tooth) thus remains constant and makes it easier for the operator to optimize his machining
- Electronic spindle load display:
- Also supports the operator in the efficient use of machine and tool capacity
- A reliable indicator to avoid damage caused by overloading
X.pos Plus - your gain in productivity, quality and comfort
- coordinate value specification
- Bolt circle pattern calculation
- Vibration filter function
- Conversion mm/inch
- 8 display languages
- calculator function
- High-resolution display with excellent readability
- High level of functional reliability under production conditions thanks to state-of-the-art electronics and a particularly robust, completely sealed housing
- During the development and selection of the electronic components, particular attention was paid to ensuring that they were largely insensitive to external interference and kept to a low temperature level
- The display colors of the background and the display can be changed and adapted to the individual wishes of the operator
- Particularly durable and practical keyboard membrane, very pleasant to use
- Furthermore, the display has a radius / diameter switch
- A data backup for the created programs is also possible according to the same principle
- Graphic support with distance-to-go display and sketch display
- Linear and non-linear length correction possible
- Easy installation, simple electrical connection and maintenance-free operation
Technical Details
WORKSPACE | |
---|---|
table mounting surface | 1370mm x 300mm |
Table load capacity (max.) | 350kg |
TRAVERSE PATHS | |
---|---|
X axis travel | 680mm |
Y axis travel | 365mm |
Z axis travel | 370mm |
VERTICAL MILLING HEAD | |
---|---|
spindle mount | ISO 40 |
quill stroke | 125mm |
Distance spindle nose - table surface | 180mm - 550mm |
Spindle speed (infinitely variable, countershaft ranges) | 50 rpm - 4000 rpm |
RAPID TRAVERSE | |
---|---|
Rapid X axis | 5000mm/min |
Rapid traverse Y-axis | 3000mm/min |
Rapid Z axis | 2000mm/min |
FEED | |
---|---|
feed rate (continuous) | 0mm/min - 1000mm/min |
Feed per spindle revolution | 0.01mm/rev - 1mm/rev |
DRIVE POWER | |
---|---|
Main drive engine power | 3.7kW |
MASS AND WEIGHT | |
---|---|
Dimensions (length x width x height) | 2.54m x 2.16m x 2.24m |
Weight | 1800kg |
Standard Equipment
- 3-axis position indicator
electronic handwheels
pneumatic tool
clamping chip tray
LED work light
coolant system
central lubrication
horizontal
guideway cover operating tool
operating manual
Options
Wide range of tooling options available
Coolant concentrate 5 l SKU: 103184
Oscillating elements LK 5 SKU: 103331
Universal facing and boring head ADA / SK40 SKU: 103404
Adapter SK40 / MK2 SKU: 103720
Adapter SK40 / MK3 SKU: 103730
Adapter SK40 / MK4 SKU: 103740
Reducing sleeve SK40 / SK30 SKU: 103750
Combination mandrel Ø16 SK 40 SKU: 103895
Combination mandrel Ø22 SK 40 SKU: 103900
Combination mandrel Ø27 SK 40 SKU: 103905
Combination mandrel Ø32 SK 40 SKU: 103910
Combination mandrel Ø40 SK 40 SKU: 103915
Accessory set ISO 40 5 pcs. SKU: 104596
Keyless chuck 1-13 mm B16 SKU: 104765
Keyless chuck 3-16 mm B18 SKU: 104770
Drill chuck holder ISO40 / B16 SKU: 104780
Drill chuck holder ISO40 / B18 SKU: 104781
Machine vice with pull-down system NZM 125 SKU: 104918
MS 125 machine vise SKU: 104955
grip type. Deluxe 16/M14 SKU: 105300
Stepped Block Assortment SKU: 105340
Set of stud bolts with T-nuts 16/M14 SKU: 105360
Lever clamp 100/M14 SKU: 105795
ER32 collet set 6 pieces SKU: 106052
ER40 collet set 15 pieces SKU: 106075
ER 32 collet chuck / shank ISO 40 SKU: 106056
ER 40 collet chuck / shank ISO 40 SKU: 106062
Milling chuck WELDON ISO 40 / Ø6 mm SKU: 106801
Milling chuck WELDON ISO 40 / Ø8 mm SKU: 106802
Milling chuck WELDON ISO 40 / Ø10 mm SKU: 106803
Milling chuck WELDON ISO 40 / Ø12 mm SKU: 106804
m illing chuck WELDON ISO 40 / Ø16 mm SKU: 106805
Milling chuck WELDON ISO 40 / Ø20 mm SKU: 106806
Milling chuck WELDON ISO 40 / Ø25 mm SKU: 106807
Milling chuck WELDON ISO 40 / Ø32 mm SKU: 106808
Indexable end mill set 25mm SKU: 107800
Shell end roughing cutter 40 SKU: 108400
Shell end roughing cutter 50 SKU: 108401
Shell end roughing cutter 63 SKU: 108402
Shell end roughing cutter 80 SKU: 108403
Shank roughing cutters 10 pcs . SKU: 108445
Boring head & boring bar set 50mm 9 pcs . SKU: 108631
Boring head & boring bar set 75mm 12 pcs . SKU: 108633
ISO 40 shank SKU: 108637
Universal dividing head HT SKU: 110953
Divider ST 130 SKU: 110960
Special accessory set / ST 130 SKU: 110970
PMS 100 precision machine vise SKU: 125012
HS 125 hydraulic machine vice SKU: 125024
INDEX facility / RT 160-320 SKU: 125805
Tailstock / RT 200/250 SKU: 125820
Round table RT 200 SKU: 125835
Wavy parallel pads 9-23mm SKU: 128960
Wavy parallel pads 25-39mm SKU: 128961
Contact us via Email for price details
Operator Training
Operator training available in showroom subject to quotation
prior to delivery. Email us to outline your needs.
Shipping
Fully inclusive shipping rates covering transportation, import customs documentation, duties
quoted for inclusion at time of order for UK mainland sites. Northern Ireland destinations, Islands
and other remote sites should seek advice prior to order via email. Clients will be responsible for
their own site offload and siting at point of use.
Finance Availability
Looking to finance your equipment?
We have access to a variety of funding sources who will look sympathetically
at requests for funding finance.
These include leading merchant banks such as asset finance specialists Close Brothers and Lombard.
The financial services division of Siemens will consider HP on the investment. Subject to Status.
On an investment of this nature with a long delivery lead time we can also look at providing a staged payment schedule.
We will confirm this with you at time of order.
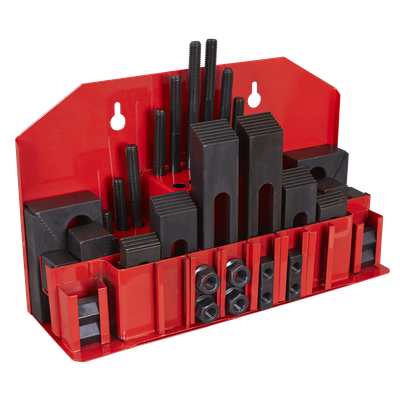
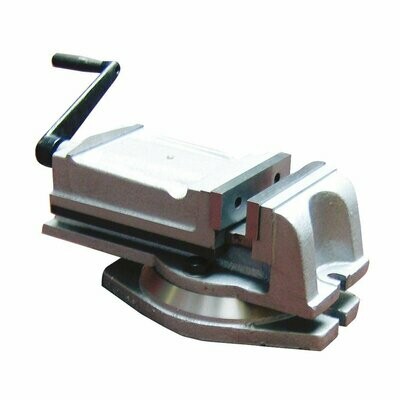
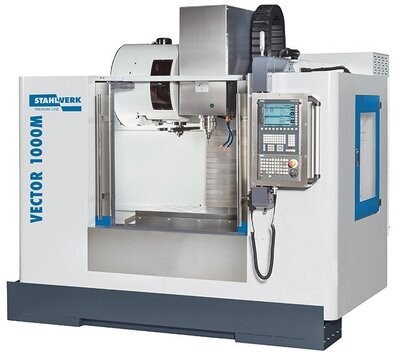